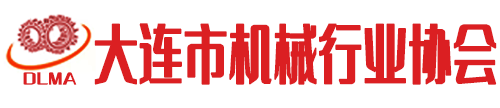
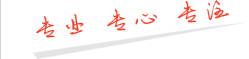
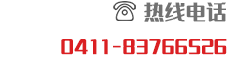
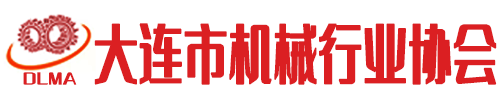
船用主机连杆新型车削装夹工艺的开发
编辑:2021-05-21 11:47:21
大连船用柴油机有限公司
栾金华 赵 涛 衣莎
摘要: 船用主机连杆是发动机的重要运动部件,车削装夹工艺的开发着重研究了车削装夹对于加工质量、工艺改进、人工、物耗的影响。结果表明:通过对车削装夹策略的不断优化,无论对车削质量的提供,加工工艺的可控性,以及对生产成本及耗材的控制方面都产生了非常积极的影响。
关键词:船用主机、连杆;车削加工;装夹;质量
船用主机连杆,是将活塞上产生的压力及惯性力传递给曲轴。作为主机动力的重要传递部件,连杆无论在材料选择及机械加工方面都提出了严格的要求。在具体的加工中,因其工件体积大、质量重,针对于车削加工的装夹方法的适用性及效率、成本都提出了较大的挑战。本文主要通过影响工件找正及装夹工艺及效率的分析,论述了装夹方式对加工效率及质量影响的主要原因,并提出了解决这一问题主要技术方案。
1 早期装夹工艺
连杆车削加工的装夹方法,通常采用的是“一夹一顶”的传统的装夹方式,这种方法是经过验证的典型的装夹工艺,它能保证较好的加工质量,以及安全性要求。但是该法方法对于不同种的工件有着不同的要求,特别是卡盘方向,如果有比较规则外圆的工件,可以直接利用卡爪对工件进行直接夹压,尾部可直接顶尖顶固。但是船用主机连杆(曲轴端)有扁平结构设计,具且中间部位镂空,无法使用卡爪,导致工件无法直接利用卡盘进行装夹,如图1所示:
图1 船用连杆加工图
连杆工件外形不利于卡盘爪直接夹压,导致夹压不稳,存在较大的安全风险。早期的连杆车削装夹工艺采用的是“胎具固定”法,即设计并制造相关专用胎具,将该胎具与连杆固定后,整体置于机床装夹,卡盘端卡爪夹固胎具,进而通过胎具对连杆整体进行夹固。该装夹工艺,无论从装夹安全角度出发,以及车削力的抵消方面,都可达到预期要求,具体装夹示意图,如图2所示:
图2 早期连杆装夹示意图
根据图2所示的连杆装夹示意图,该种装夹方法虽然能满足装夹的最基本的安全及夹紧力方法的要求,但经过实际运用,所反应出的具体问题还是比较突出的。首先,该胎具在设计上虽然满足了安全性及刚性的要求,但没有考虑到该胎具质量大,体积大,单人无法独立完成其安装及拆卸,需要两名操作者,并借助吊车才能完成胎具的安装工作,耗时,耗力,耗物,整体效率不高。另外,该胎具在与工件的定位及连接需要前期连杆本体的工艺孔进行物理结构的支持,即连杆与胎具连接面需要事先加工出满足尺寸及粗糙度要求的工艺孔,该孔需要仔细计算,必须为最终成品孔留足加工余量的前提下,还必须保证定位销孔与螺纹底孔的同轴度要求,这对于事先的工艺计算及镗床的加工精度要求都是比较高的,同样对于胎具定位销孔的加工精度及形位要求也是等同的,该装夹方法对于工艺孔及定位胎具的加工精度要求是超出实际预想的,需要进行较多的工艺干预及加工装备,并且对于每种机型的连杆都需要制造该机型连杆所专用的胎具、定位销孔,以及相应的工艺孔加工规范,整体过程过于繁琐,并且对辅助工序依赖程序较大,虽然满足了基本的装夹及切削要求,但该装夹方法由于上述两方法的局限性,无论在加工的整体效率及加成本控制的方法,都未能达到预期的理想效果。
2 装夹工艺的创新开发
采用传统的定位胎具进行车床加工的装夹,虽然满足了基本的加工要求,但在效率、加工成本的控制,以及人工劳动强度的侧重力度还是不够的,难以摆脱缺点,无法体现装夹工艺的优点。所以需要对装夹工艺进行创新式开发。根据以往对早期装夹工艺的实际使用效果进行了分析,我们意识到,以往的装夹胎具,体积大,重量大,需涉及辅助安装设备,并且无法单人完成,并且对工件及胎具的工艺孔有严格的尺寸及形位公差要求,实际操作加工质量比较困难,人为的增加了加工成本,这都是以往装夹方工存在的不足之处。针对这些实际产生的问题,我们需要开发出一整套全新的装夹工艺,它必须满足:重量轻,体积小,易于安装,无需额外的工艺孔加工要求。基于上述理论,我们制定了相关的方案:即将以往笨重的定位胎具完全摒弃掉,而用结构更为简单、轻便的焊接夹胎,上、下各一个安装在对称卡爪上面,通过夹胎将连杆曲柄销端已经粗铣的扁部位夹紧,另外两点卡爪撑紧工件瓦孔,轴向方面可以利用为镗床工序预留的装夹孔,安装简易的定位块进行轴向固定,如图3 所示:
图3 新型连杆装夹装置想像图
从上图中,可以看到,在保证整体刚性及强度的前提下,我们采用了材料及成本更为普及成本更为低廉的普通铸钢材料,该材料不但满足了我们所需要的机械性能,并且具有很好的焊接性,为我们的备料及相关胎具的定型工作提供了很大的选择空间,并且制造起来也比较简单,快捷,夹胎的制造工差及形位公差要求极低,有较强的宽容度。
该夹胎在设计定型时,优点还在于它可以根据主机连杆尺寸相近的范围内,可以只制造一种夹胎即可满足2-3种的主机连杆车削装夹要求,展现了很好的兼容性及经济性。
图4 新型连杆装夹装置实际工作图
通过新型夹胎,很好的解决了工件径向装夹的约束要求,那么为了解决装夹中轴向的约束,我们利用上道工序中,为镗床留下了装夹工艺孔,设计了一组阶梯轴垫,该轴垫装入工艺孔中,另一端顶压在卡盘面上,通过尾座的顶尖压力,使整个工件顶靠在卡盘上,很好的解决了工件装夹轴向的约束问题。
该新型夹胎设计简单,便于制造,轻巧简便,只有一名操作者在吊车的配合下,即可一次完成一台主机连杆(6-7根)的夹胎安装工作,装夹效率大大提升,而且摆脱了工艺孔及定位销的依赖,在整体的加工工艺中可以减轻上道工序的大量工作。可以说新型夹胎无论在制造成本、装夹效率、还是整体的工艺成本控制方面都有着很好的提升与进步。
3 装夹装置的深入改进策略
经过对该新型夹具的实际使用情况跟踪,我们发现:虽然新开发的夹具很好的解决了夹胎装置的轻量化等问题,但是在轴向方面的定位块不能很好的约束工件轴向力,导致加工质量不稳定。
根据现场对装夹装配的进一步研究分析,我们发现由于上道工序中,在加工镗床预留装夹工艺孔时,并未将连杆曲柄销端端面进行铣平加工,致使工件被顶紧后轴垫出现偏置,即一面接触到卡盘面,另一面出现悬空现象,导致两个约束轴的形位公差不达标,,进而影响连杆整体的车削加工质量。
鉴于此原因,我们认为,两处约束轴向力的方法存在缺点,且过于依赖上道工序,没有根本上解决整体装夹的通用性与宽容度要求,有必要完全抛开对于工艺面和工艺孔的依赖,从而彻底掌握装夹的主动性。我们认为:轴类件中,单点定位好于两点或多点定位,因为多点定位会产生很多的不确定因素,甚至会使工件产生过定位,影响工件的整体切削质量。
于是我们考虑将轴向约束力有两点改为单点,即制作一个顶杆,头部为圆弧形设计,置定于卡盘中心,装夹工件时圆弧部分顶于连杆瓦孔内壁,与尾座顶尖力组合成工件的轴向约束条件。至此,整体的优化策略完成,下图为该改进策略的具体实际应用情况:
图5 装夹装置改进后实际工作图
4 结论
船用连杆中的车削装夹工艺性直接影响连杆车削装夹的整体质量。我们通过自主研发、设计、制造及改进,形成了一整套科学有效的装夹工艺及装置,不仅解决了装夹的实际性需求,也减少了工人的劳动强度,在保证整体加工质量的同时,也提高了加工效率,大大降低了生产成本。
参 考 文 献
[1] 鄂中凯,机械设计手册,新版.机械工业出版社,2006
[2] 曾正明,机械工程材料手删(金属材料),机械工业出版社,2005.6
[3] 樊铁镔、李振加、刘玉福、李德森,重型切削实用技术手删,机械工业出版社,199
CONTACT US
秘书长 0411-83766521
综合部 0411-83766525 0411-83766526(传真)
信息部 0411-83766526 0411-83766526(传真)
联络部 0411-83766523 0411-83766523(传真)
地址:大连市沙河口区振工街28号
(Z28时尚硅谷2号楼2303室)
邮编:116021
邮箱:dljxlhw@163.com